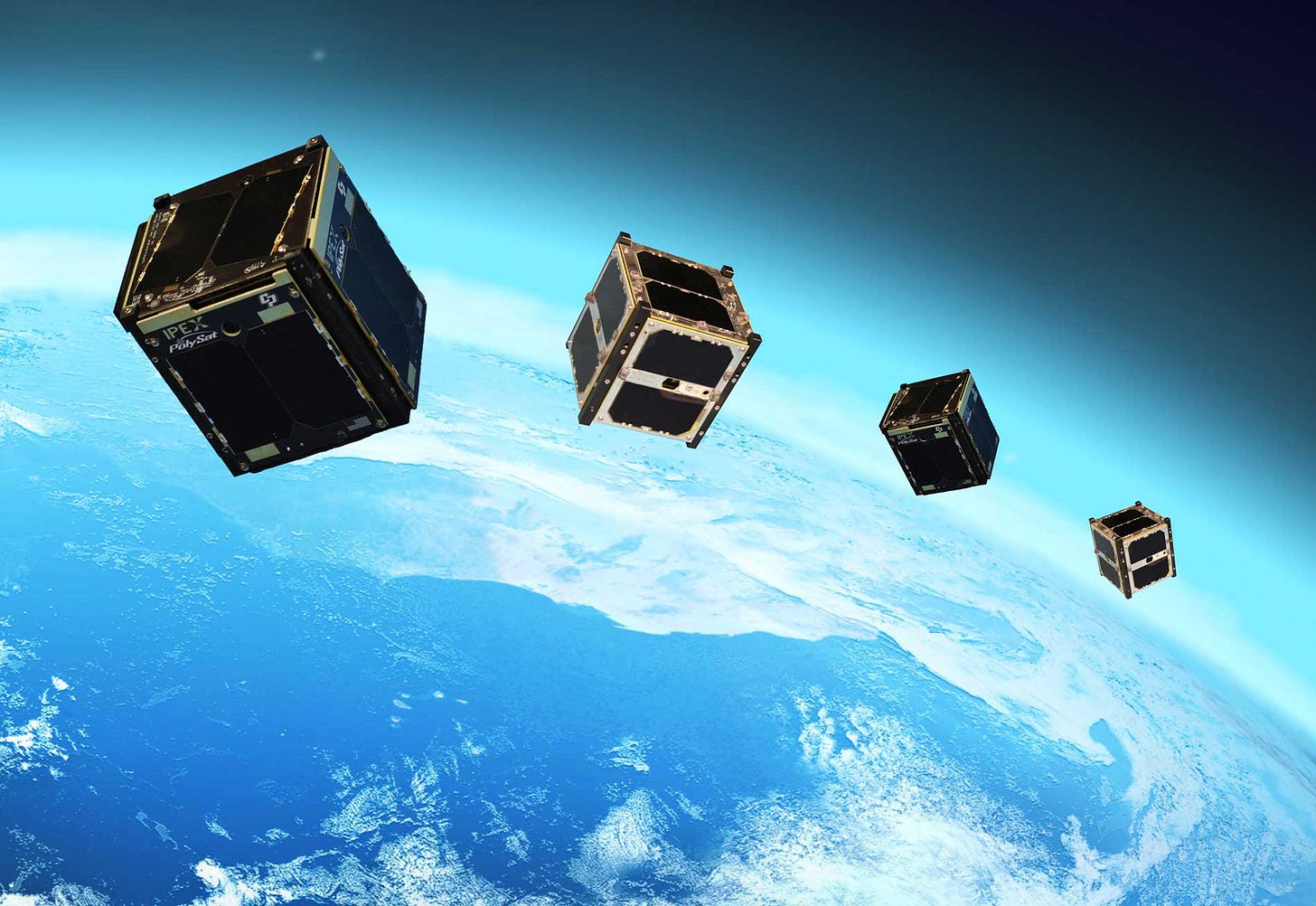
For most of my undergrad, I had somehow gotten known as the āsatellite girl.ā Maybe it was because I tried to get involved in as many clubs, projects, and internships that would teach me anything and everything about space. My senior thesis was building a GNC (Guidance, Navigation, and Control) subsystem for a 6U cube satellite. My masterās dissertation focused on applying Federated Learning in satellite constellations. Well, now Iām even starting a PhD in Aeronautics and Astronautics. Okay, maybe I do have a bit of love for space š .
However, most people are surprised when I tell themĀ I never had my sights set on pursuing a career in aerospace before college.Ā I first came in as a civil engineer, and I wasnāt even aware of what satellites were or what complexities they would soon introduce to our current space community. From problems ranging from space sustainability, space traffic management, and space domain awareness, this is probably one of the most exciting times to work in this field. But, I didnāt know this as a small first year in college.
My first inklings of any interest in aerospace actually came fromĀ joining my undergrad cube satellite team. Somehow, I was put as a project manager of that team in my first year. (As you can tell, there werenāt many people in the aerospace community when I first joined.)
Going into our first meeting, I was unfamiliar with even theĀ meaning of the cubeĀ in cube satellites. I didnāt realize that Iād face aĀ HUGEĀ learning curve trying to understand how this spacecraft the size of a tissue box operates. However, I grew to love our project. I stayed on the team for all four years of my undergrad and eventually rose to become our chief engineer. I was now familiar with all the ins and outs of each sub-system of the cube satellite and how they needed to interact with one another, starting from the mission design phase all the way to launch and operation.
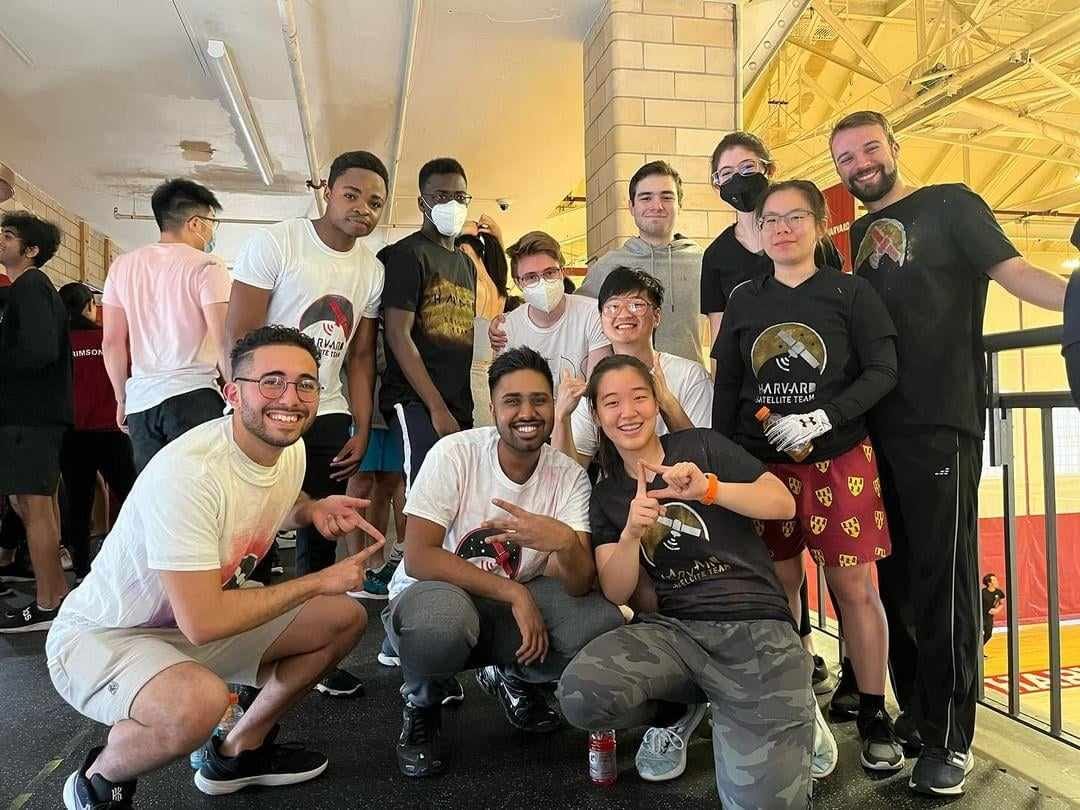
Over the course of this article, Iām going to touch on four different topics:
What is a Cube Satellite, and Why Build it?
Breaking it Down: The Key Subsystems
Real-Life Applications Into Industry
Building a Cube Satellite, Where to Start
Hopefully, by the end, I can convince you that cube satellites are pretty cool š. Maybe you'll end up joining or starting a club at your school, too!
What is a Cube Satellite, and Why Build it?
First of all, in case you arenāt familiar, cube satellites⦠What are they? Why should we build them? And if youāre interested in aerospaceĀ or want to try dipping your toes into them,Ā why should you join your college or high school cube satellite team?
Cube satellites, dubbed lovingly by the community asĀ CubeSats, are a type of nano/microsatellite with a standard size and form factor. These satellites are built to fit into cubes described in sizes of Us, with each U representing a volume of a 10x10x10cm cube. Youāll often see sizes of cube sats referred to in this manner, where a 1U satellite represents a 10x10x10cm cube, while a 2U is a 20x10x10cm cube, a 3U being a 30x10x10cm cube, a 6U being a 20x30x10 cm cube, and so on and so on.Ā These satellite sizes are standardized to both ease the storage and deployment processes of these small spacecraft.
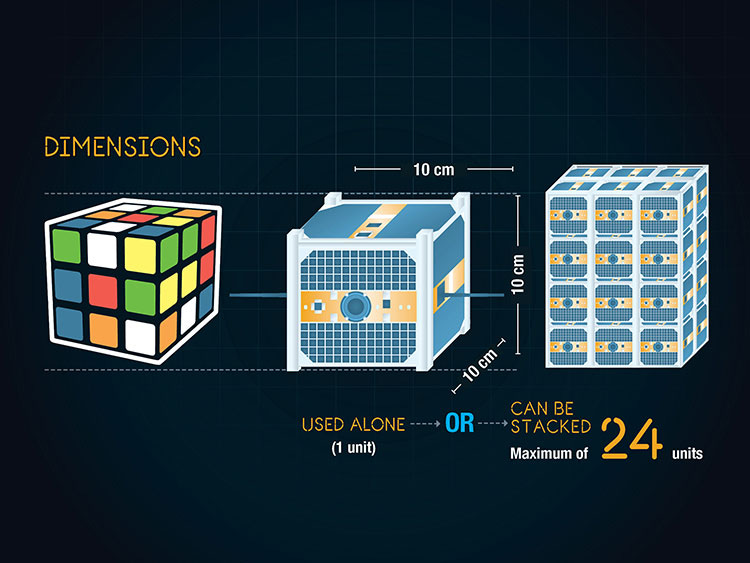
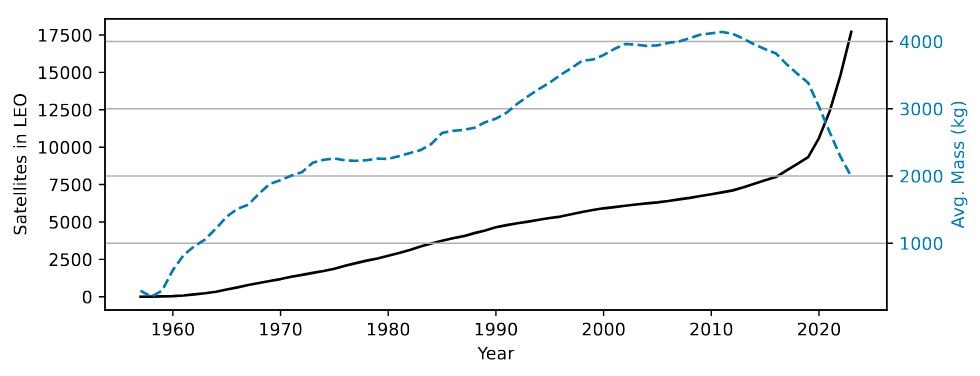
Due to how small, modular, and cheap it is to build these CubeSats, the barrier of entry into the current aerospace community has been lowered much more than ever before. This cube-shaped design has been widely adopted by college aerospace communities, research labs, and small startups in the community, skyrocketing šĀ the number of spacecraft entering the Low Earth Orbital (LEO) regions over the past 10 years. Now, even without the support of larger government or industry players, these smaller aerospace communities can build their own spacecraft to host their payloads in space,Ā the scientific mission/device mounted on the spacecraft.
Although these CubeSats are extremely small compared to popular satellites such as those found in SpaceXās Starlink constellation (which, when fully deployed, they span up to 100 feet, or a third of a football field) youāll find thatĀ these small cubes are small and mighty.Ā They have most, if not allĀ the core capabilities that a larger satellite needs to function.
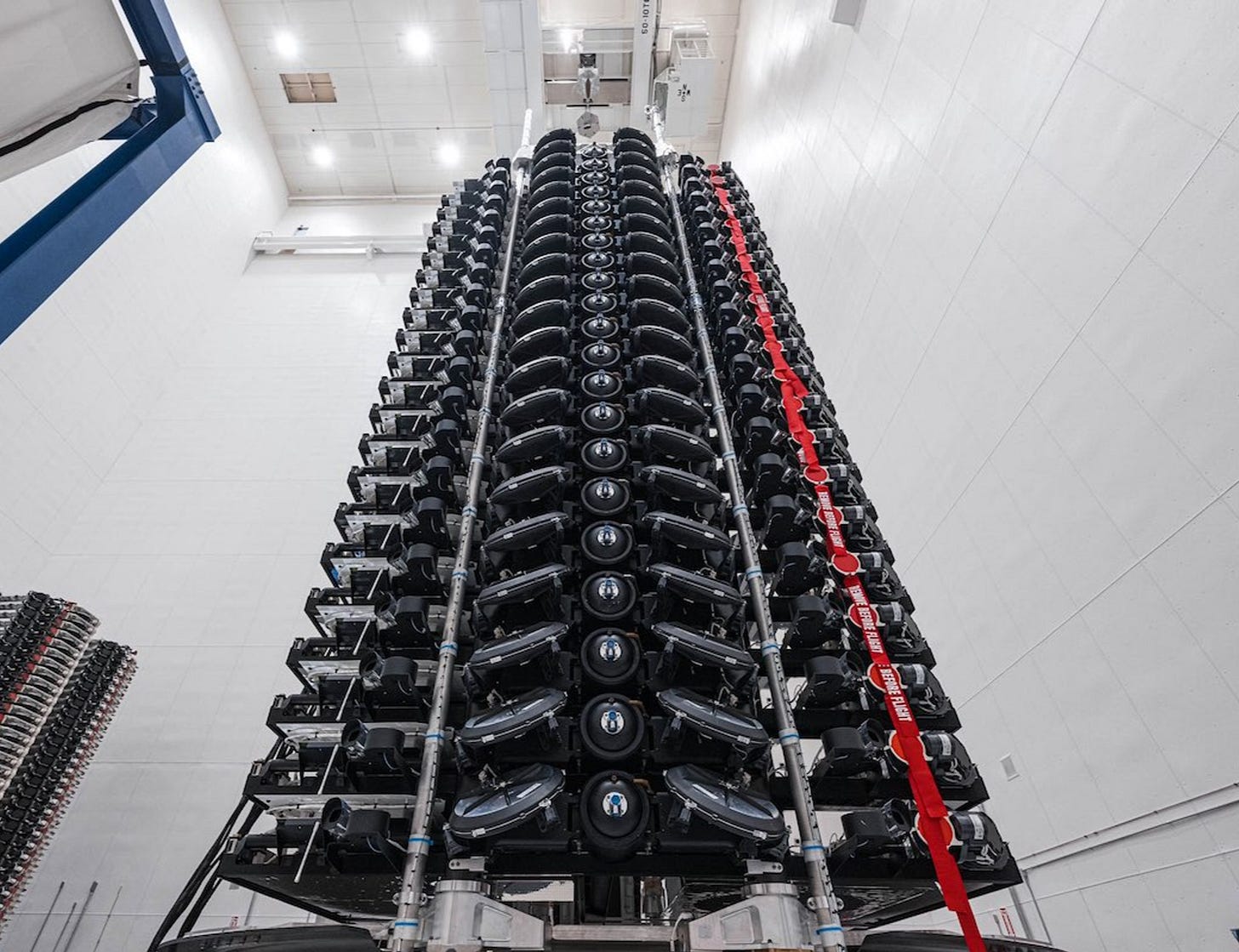
This is why I believe CubeSats are incredibly well-suited for university cube satellite teams. Despite being much smaller in size, the process of building a CubeSat allows college engineering teams to be introduced to many key concepts, subsystems, and environmental constraints that are specific to designing space-rated vehicles. For example, when choosing electronic components for different subsystems, now you need to consider whether or not the board is radiation tested š. When looking at thermal regulation, youāll find complications in heat transfer from being in the vacuum of space- no air šØ, or convection, is available to cool components down. Even before starting the development process, all teams will find that their payload will introduce constraints š that will dictate key design decisions for their spacecraft. (This could range from specifics in orbit trajectory design, hardware component selection, spacecraft size/volume, and so many more!)
Compared to other engineering teams focused on space initiatives such as rockets and weather balloons (which are also incredibly cool!) satellites have a much longer lifecycle for mission design, manufacturing, and operation than their popular project counterparts. This encourages college teams to structure themselves to span multiple cohorts of years and build a team environment focused on teaching and transferring essential skills/lessons to the next group of undergrads, continuing the mission.
Depending on when a student joins a CubeSat team, they may find themselves focused on a completely different mission stage compared to students who joined just a few months prior. As the team moves continuously through the spacecraft development process, it will be hard to find any dull moments. The completion of the design phase leads to the manufacturing. After completing all subsystems, one moves into integration. With a fully assembled satellite, there is testing (vibration, thermal, etc.). Then, finally, once the cube satellite is approved to be launched on the rocket, one must think about operations and control throughout the spacecraftās mission lifetime. For most university teams, building a cube satellite is truly a multi-generation endeavor (if you consider each graduating cohort to be 4 years ā°). This makes it all the more important to ensure the team prioritizes building and maintaining institutional knowledge and invests in training each new generation of engineers š¶Ā that join the team.
Breaking it Down: The Key Subsystems
Now that you understand what a cube satellite is and why it would be built, letās dive a bit deeper into the inner workings of this device. Here is a quick rundown of most of the subsystems youāll need on a cube satellite:
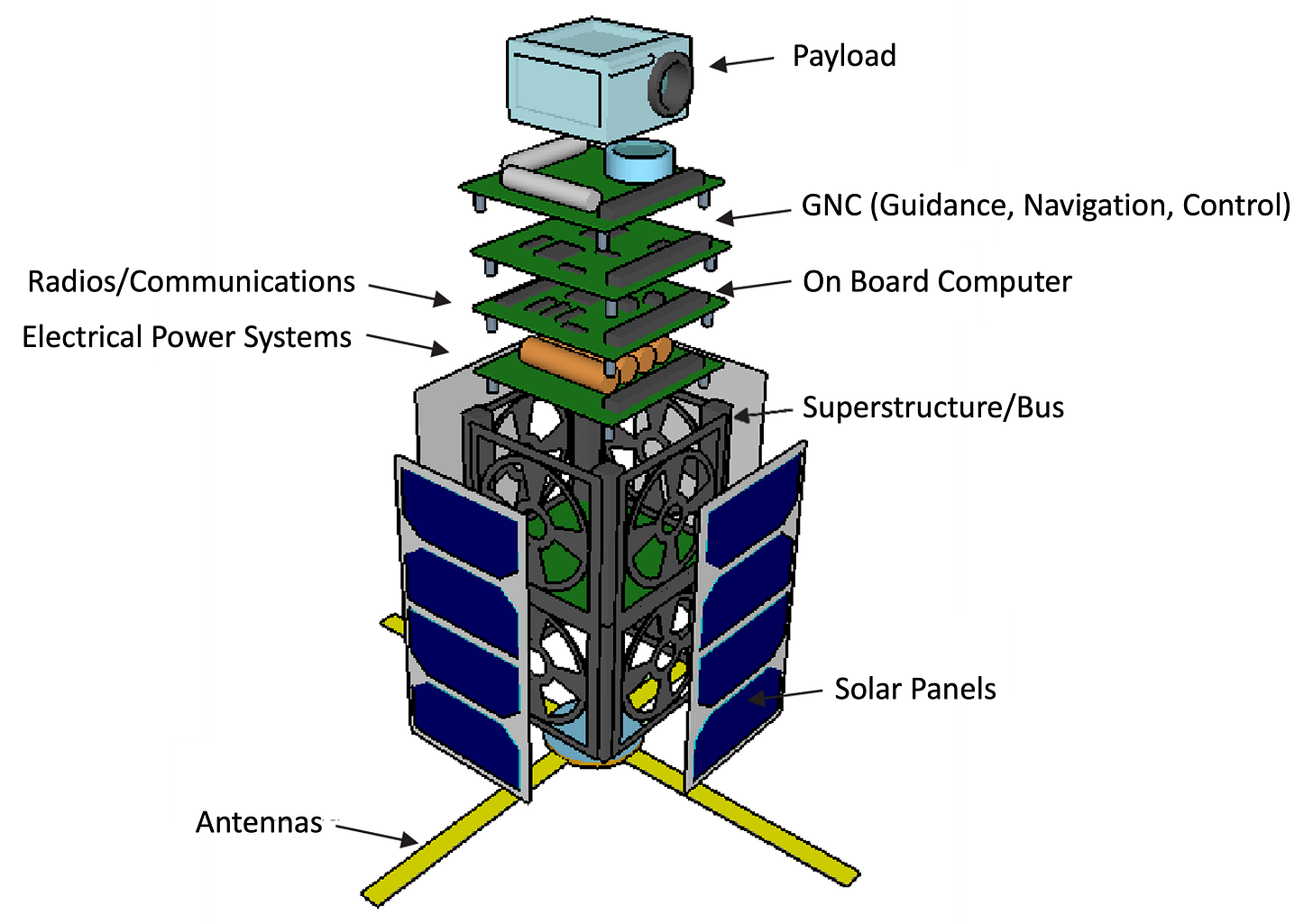
Guidance, Navigation, and Control (GNC) - this is one of my personal favorites, (not just because this was my senior undergrad thesis) because it truly is one of the most complicated subsystems on a cube satellite. This subsystem is in charge of:
All sensors (star trackers, sun sensors, IMUs), needed to determine the spacecraft position and orientation in orbit
All actuators (reaction wheels, solar sails, magnetorquers) that are used to orient and point the spacecraft towards a specific direction.
These sensors and actuators need to work together to reach specific pointing requirements for the mission, which typically is driven by the need to orient the spacecraft to different locations with a specific level of accuracy (for instance: reach a pointing accuracy of 5 degrees towards a ground station on earth for communication purposes). Integrating all of these components was definitely the most difficult part, as all of the moving (and even static) pieces needed to harmonize completely to ensure measurements didnāt propagate throughout the system. Like, consider the following situation. If our sensors were only accurate to the point of 5 degrees, weād never be able to meet our pointing requirements with even a slight imperfection in the performance of our actuators.
Electrical Power System (EPS) - The EPS is in charge of the power generation and storage capabilities, providing power to all other other subsystems. There are solar panels, batteries, power management circuits, that all must be rated to fully support the CubeSat throughout the spacecraftās daily energy necessities.
With the Solar Panels of the cube satellite, you can build further complexity into the system by incorporating deployment mechanisms to could maximize the surface area facing directly towards the sun. Otherwise, most cube satellites have their solar panels mounted directly onto the frame of the satellite, plastered on as many faces of the CubeSat as possible to allow for constant solar power generation. For our cube satellite, we actually tried to custom-build our solar panels, buying the individual solar cells and arranging them in formations of series and parallel circuits to maximize solar power generation.
The Battery Board, stores all of the electrical energy from the solar panels, and supplies these to all of the subsystems throughout all operation sequences. An important piece of the batteries, however, is providing power when the solar panels cannot. This is especially so when the spacecraft is hidden behind the Earthās shadow, as the batteries must be capable of storing enough power for the dark periods with no sun available to provide solar energy.
Communications, Radios, Antennas - how we play telephone with our satellite. The communications subsystem allows CubeSats to transmit and receive data from ground stations. If you arenāt familiar with ground stations, think of them as a radio station on Earth that sends commands and receives data from spacecraft flying directly above the facilityās location. This subsystem includes antennas and transceivers, which may need upgrades/modifications depending on the frequency band used to communicate through.
The antennas are selected to send signals along the specific frequencies selected to use for the mission comms. These typically lie in the UHF (378-870 MHz) and VHF (49-216 MHz) ranges.
The transceiver needs to be able to handle data rates for any images or scientific measurements that are sent back from the payload. When testing the Lora radios for our satellite, we realized that the specific frequency band we would be using could only send ~1.6 KBs of data per second. This meant to send a single smartphone image (assuming 2MB), with passes ranging from ~5 minutes over the ground station each orbit, we would need to have our satellite pass at least four times overhead to receive the full image. This could take multiple days, depending on where your ground station is located! Now THATās a long lag time.
On Board Computer (OBC) - The ābrainā š§ of the cube satellite, the on board computer is in charge of commanding the different subsystems to perform actions needed by the spacecraft to go into its different mission operation states. This could range from carrying out:
communications protocols š” back to earth
activating deployment sequences š¤ for payloads
generating power š through solar panels
activating idle states š for power conservation, and many more
Typically, cube satellites used to have multiple avionics boards, with one for each subsystem that needed to complete different tasks (ex: a separate GNC, EPS, and Comms boards). But there has been some shifts with the development of an all-in-one OBC board, such as the PyCubed (our Harvard Satellite Team (HST) used this for our project), which you can now use to replace the functionality of all the boards typically found on a traditional avionics stack. Due to this being an open-source design, anyone can take the board's schematics, buy all of the components, and start soldering, picking, and placing the different components on this board. We did this on our cube satellite team, which took a grueling ~20+ hours in total to complete the various boards.
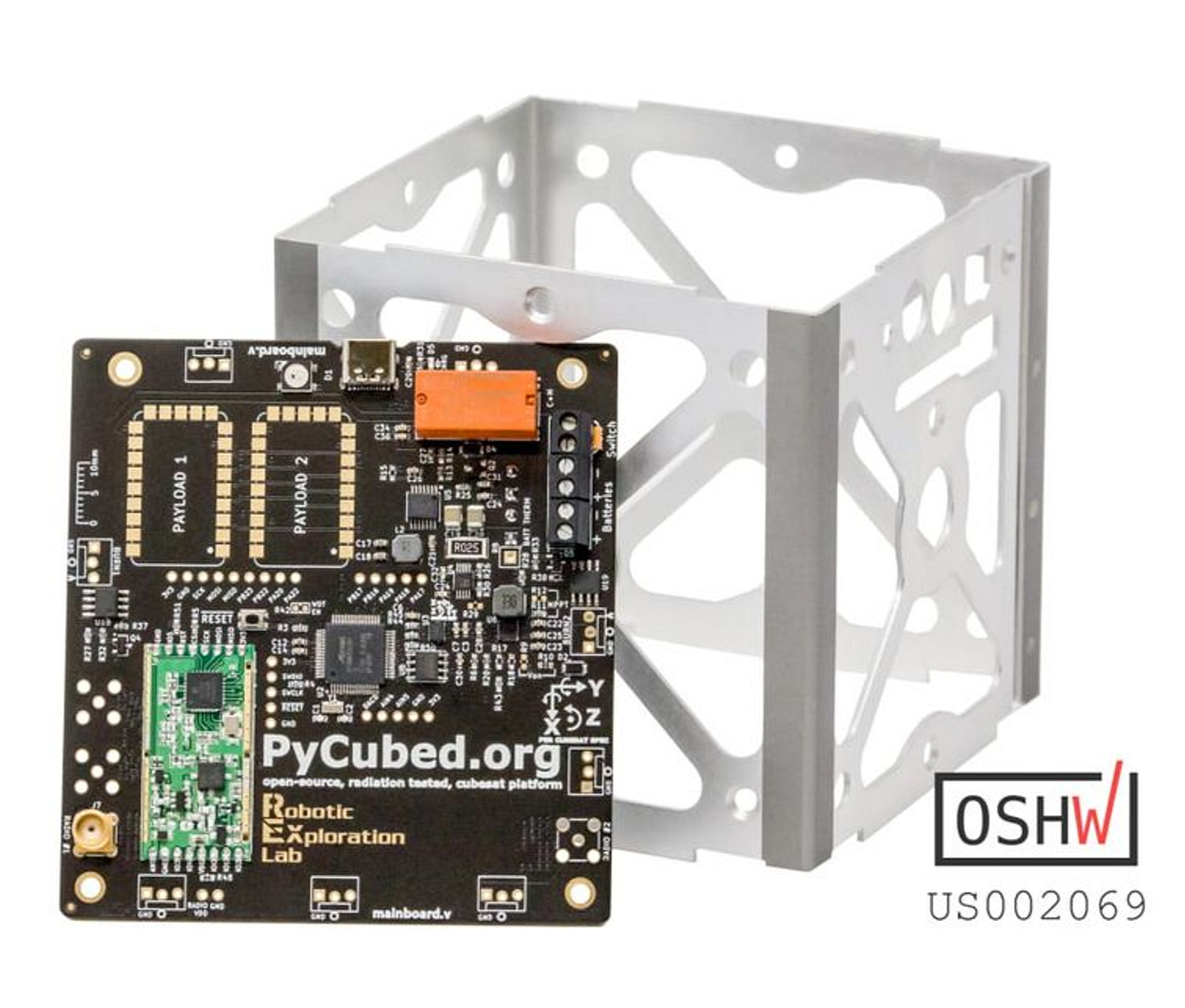
Superstructure - Referred to as the bus, the structural subsystem, or just the frame of the CubeSat, the superstructure provides the skeleton for all other subsystems to be attached onto. As the only structural piece of the entire spacecraft, it must be strong enough to withstand the intense vibrations during launch, and provide a significant chunk of the surfaces available for radiating the thermal buildup from electronic components. Although the frame must be strong, it must also be light to minimize the launch costs of the cube satellite.
For the superstructure of the Harvard Satellite Team, we had the luxury of being provided with the design of a graduating seniorās cube satellite superstructure, which allowed us to save lots of time on the design process of this component. Built in a very modular manner, the satellite size could be easily modified from a 1U to a 2U, with an endplate and rails architecture.
Payload - as mentioned before, the payload is the scientific mission or experiment carried by the CubeSat. Depending on the objectives of the specific mission, it can range from extensive cameras, sensors, or other scientific instruments to help monitor storms and improve weather accuracy forecasts, collect dust particles to send back to Earth, and so many more. Specifically for our cube satellite team, we focused on manufacturing a 2U cube satellite to test a novel student-designed sun-tracking nitinol (Shape Memory Alloy) actuated solar panel payload.
To get one of these into space, however, you will need a launch vehicle to hitch-hike a ride on. One of the largest opportunities for this is NASAās CubeSat Launch Initiative, also known as NASA CSLI, which provides college and high school CubeSat teams a chance to have their spacecraft fly onboard upcoming launches. Through this, you can finally complete the full lifecycle of the cube satellite itself and gain actual hands-on flight operation experiences of a little tissue-box-sized satellite you built and launched into space!
For our team, the cube satellite initiative I joined started just the year before my freshman year of college. After two failed applications, we finally were awarded a launch on NASAās Cube Satellite Launch Initiative (CSLI) on our third application attempt in my senior year! As they say, third timeās the charm š. Usually, these calls for applications will have you specify why your satellite payload proposal would be a technical innovation and provide some scientific / engineering novelty to the research community. Since our teamās payload was designed directly from our students, it was difficult to generate ideas that needed larger domain expertise, knowledge, and resources typically found in proposals from research groups and labs. This led us to stick with concepts/materials that were widely used within the space community, specifically - Shape Memory Alloys (SMAs) - but in ways that were not typical to the traditional designs that use the material.
SMAs, are alloys that can remember their āoriginalā pre-deformed shape whenever heated to a specific temperature. However, the difficulty of reusing these SMAs is the need to physically deform the structure each time we want to reset the actuator. Setting the reshaping form of these thin wire SMAs into a spring-like figure, we implemented a design focused on the SMA reusability by having two SMAs actively pull against one another, physically deforming its partner to āresetā the de-actuated state. This was used to rotate/orient a solar panel rested on a spherical joint platform to provide sun-tracking capabilities to the payload itself.
A really cool video that kind of dives in deep about SMAs is shown here:
Real Life Applications Into Industry
I bet youāre all wondering, how well do these experiences translate to working in industry? What are some similarities and differences?
Well, in my experience, the first thing I would mention is that working on a CubeSat throughout my undergrad led me to get many of the internships Iāve had at various space companies. (Itās actually how I landed my internship at SpaceX). Whenever I get asked how Iāve been able to break into aerospace, or land these internships roles, I always tell everyone:Ā start working on a technical project team.
Iām using cube satellites as an example (because these are near and dear to my heart), but the project can honestly be anything. Join the rocketry team. Join your robotics team. Join your racing team if you have one.Ā Are there not that many engineering project teams at your school?Ā Well, why not just make one?Ā It doesnāt take too many people to start.
The reason why these employers are looking for these types of interns is that so many translatable lessons and experiences come from building these smaller-scale CubeSats to production line satellites deployed in the thousands. Theyāre looking for students that are not just book smart but kids who know what itās like to get their hands dirty. Students whoāve experienced firsthand the painful lifecycle of finishing an engineering project from project ideation, design, manufacturing, testing,Ā continuousĀ iteration, and finally operation. They want to see how you learn and overcome moments when your first, second, and third designs all fail, but you still come back to keep working until you find a design that finally works. There are also certain things that you can only learn through direct project experience. As a mechanical engineer, for instance, you only see the importance of tolerances and designing for assembly once you come to integrate all of your hand-machined parts and realize you canāt fit anything together cause you didnāt set the right tolerances.
These people know how invaluable these technical projects can be not only in improving your engineering knowledge, but also in providing you the firsthand experience of what itās like to try and complete an engineering design project. All of my managers have told me theyād rather take an engineer with a low GPA with lots of project experience compared to a straight-A student who has never walked into a machine shop / finished their own technical project before. Theory and equations always tell you the āprettierā story. Itās only when you dive into the hardware that you realize sad things like:
I canāt ignore friction!?!?!?
The 3D printer actually prints like a millimeter too thick, now nothing fitsā¦
What do you mean my Raspberry Pi wasnāt flashed correctly?
Ohhhh so thatās what they mean by design for manufacturing toolsĀ andĀ assembly
Yeah, you learn a lot.
However, Iām not going to lieāit takes a lot of time and effort. And trust me, I realized immediately from that first satellite team meeting that building a cube satellite (from scratch) is hard.Ā Really hard.
Youāll spend many long days in the engineering buildings, eyes red from trying to debug a flight software script that was working just a few days ago, but for some magical reason, it doesnāt work now. You swear you havenāt touched it. But it happens. At some point, you might find that you didnāt fully understand the concepts you learned from class, and you need to relearn some things to try and make sense of the project youāre working on now. You find yourself asking many tough questions, such as whether it is worth sacrificing this component to cut down on costs or trying to find a way to build it cheaper. You need to be constantly curious and realize itās important to ask for help regularly (whether from mentors, other engineering project teams at different schools, or outside industry partners). Youāll hate design reviews but realize itās incredibly useful to have them (please always try to get feedback on designs).
Although I donāt know if Iām selling this very well, I hope you are now convinced (and hopefully excited?) to join your own high school/college cube sat team. Or just any other engineering project group thatās available to you. Iāll be happy if you just join an engineering team š
Jokes and scary warnings aside, though, it truly is such a fun experience. The satisfaction you get when you see all the different components working together side by side, the first time your radios work, getting that oh so perfectly toleranced piece after that long CNC machining session, thereās so little else that can compare to the joy you feel from these moments. And as a bonus, youāll come out of this as aĀ muchĀ better engineer. Truly. Thereās a limit to how much youāll gain from just your textbooks.Ā Real-life experiences can and will teach you so many more things.Ā Go out there! Start your own project! Get your hands dirty, and see all the cool things you can make!
Building a Cube Satellite, Where to Start
Okay you got me, but I donāt know even where to start building a CubeSat. Where do I even start?
That is a great question. Although this may not be the most comprehensive overview, Iāll drop you a few resources and links to try and look at where to start.
For just a general understanding of cube satellites:
Explanation of cube satellite subsystems, a really good medium article
CubeSat 101: Basic Concepts and Processes for First-Time CubeSat Developers
A list of all CubeSat Launch Initiative Resources from the Kennedy Space Center
Trying to build a cube satellite? Cool resources:
NASA State-of-the-Art of Small Spacecraft Technology Report
Provides lists of vendors that can provide different subsystem components, and just a great overview on each subsystem as well if you wanted to learn more
PyCubed - an open source on board computer specific to cube satellites!
So many YouTube videos, but there is this cool YouTube series that tried to build a CubeSat under 1000 dollars
You want to launch your own satellite? Check this out:
Where to meet cool space people to talk about CubeSats, and try to get funding from:
SEDS - Students for the Exploration and Development of Space
They also host an annual conference called SpaceVision that is great, and also provide small grants for teams
Ask to join their discord! Really great community of students working on CubeSats, rocketry, weather balloons, any space project in general!
Check out any labs at your school, see if they need anyone to build a bus for a payload they want to test! All you have to do is make the CubeSat, they provide the scientific mission.
Lots and lots of companies! The help they can give you ranges from funding, mentorship, and really cool experiences on their campus sites! We had some support from folks at SpaceX, Blue Origin, Ansys, and General Atomics at different points of our mission.
This was definitely a lot of things to throw into one post. I thank you if youāve made it this far.
But I hope you have a better idea of what cube satellites are now and a bit more of an appreciation of these small beeping cubes that are shot into space. Once you learn more about these systems, youāll be truly open to all of the incredibly cool, amazing things you can accomplish by combining just a few components into a small metal frame. So now, go join or make your own cube sat group! Start your own journey into aerospace! Or, take some time to read some more really cool articles on the Overview š.